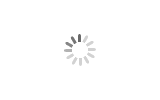
- : KAIZHENG
- : CHINA
- : To be confirmed
- : Sufficient
The high pressure granulating is a vital technological breakthough in the process of grinding with roller press. This technique is wide applied in cement and mineral processing industries.
Grinding Roller Press Applied materials: Cement clinker,Raw cement materials (limestone, clay),Slag,Titanium oxide,Mineral,Synthetic fiber.
Applied materials: Cement clinker, Raw cement materials (limestone, clay), Slag, Titanium oxide, Mineral, Synthetic fiber.
Process:
Based on the experience in designing the series of high pressure roller extrusion equipments, we have developed a special machine for grinding and granulating. It is suitable for both pulverable material and unbreakable material. There is a wide range of granularity of the output, when it is used for grinding. The grinding with roller press can operate individually or with ball mill. It aims for minimising the energy consumption during grinding process, and for cutting the operation cost.
Comparing with the traditional technique:
Energy saving up to 30%.
The production of granular material increased from 30% to 50%.
The expanse on installation,operation and maintenance drops significantly.
The grinding with roller press can be installed in a new factory or can be upgraded and transformed based on old equipment.
The main structure of grinding with roller press, is that the two counter-rotating rollers. The one is fixed and another is not, movable roller is supported by hydraulic system on the rack. The surface of rollers are specially treated, in order to increase their strength and abrasive resistance. The material will be granulated when it is continuously feeded to the rollers. The design basis of compactor has to consider material's characteristics and operating method. For instance, when it is used for grinding, we need to analysis its granularity composition and hardness. When it is used for seperating the unbreakable material, we need to know its maximum particle size.
Technical features:
Two transmission systems: For the smaller machine it adopts motor--reducer--synchronous gear box with decelerated twin shafts--two rollers. For the bigger machine it uses two motors--reducer--two rollers. It belongs to pure torque output. The selection of roller material is depends on the applied material and client's requirement. It can be a tungsten carbide pin structure or a meningeal material surface welding structure.
Technique of roller protection:
No matter for briquetting machine, compactor or grinding with roller press, roller material and its surface treatment is vital as the most vulnerable parts are those two rollers.
As to briquetting machine, referring to the difference of material we have bearing steel, tool steel and stainless steel.
As to compactor, its abrasive resistance and compaction ability enhanced by doing special roller surface treatment.
As to grinding with roller press, the roller surface uses a tungsten carbide pin structure or a meningeal material surface welding structure, to improve the abrasive resistance and compaction ability.
Technical parameters: